Some Royal Mail drivers suffer from a poor image with the public – one of vans rushing around towns and cities in a red blur.
But it’s a largely unjustified perception of today’s Royal Mail driver, according to Nick Bridle, Royal Mail’s Area Transport Manager for Hants & Dorset. And he has the statistics to prove it.
Bridle joined the Royal Mail fleet strategic projects team in 1992. His initiatives include telematics, driver risk assessment, and external benchmarking and workshop management systems deployment.
It led to the creation of robust system for monitoring and measuring the performance of the fleet, the drivers and individual vehicles.
Telematics has now been installed on around one-third of the Royal Mail fleet. That’s 8,000 vans and trucks up to 7.5 tonnes pumping back a wealth of vital data.
By better understanding vehicle utilisation and clearly seeing on the report where one vehicle can take on the work of another, Royal Mail operational managers have been able to remove 5% of vehicles from the fleet on a national basis during 2008, with around 35% being trucks up to 7.5 tonnes.
In Bridle’s local area Royal Mail has managed to reduce the fleet by 50 vehicles, which represent 10% of the local fleet fitted with telematics. This has led to significant whole life cost savings for the fleet.
Baseline data is still being assessed, but the Royal Mail has also seen average fuel consumption improve through linking harsh braking & speeding data with communication of defensive driving techniques.
Risk assessments have also been carried out on more than 10,000 drivers during the previous year which has supported a reduction in the number of reported accidents, down by around 10% during the period.
Unreported damage costs and non fair wear & tear have been halved over the past five years through the deployment of a fleet scorecard which focuses on agreed key measures.
“Telemetry is management by fact. You have a plan and can demonstrate the actual performance versus the plan, Bridle says.
In his local area there are more reported accidents in summer rather than winter. As a result, the high impacting units are being targeted and agreed action taken.
“We work with the drivers to influence them. We identify the issues and pull the data into our plan for the unit,” Bridle says. “We aren’t penalising them; we want to keep them driving and keep them safe – it’s about driver awareness and performance improvement.
And if I improve safety, I reduce cost.”
Bridle benchmarks his Royal Mail performance against other fleets, including Tesco.com, Centrica and Allied Bakeries.
“You have to share best practice and be prepared to use best practice to generate real improvement,” he adds.
KPIs include third party collisions, blameworthy percentage, annual mileage (the Royal Mail fleet covered 600 million miles last year, while the 8,000 vehicles fitted with telematics travel 10 million miles per month), and incident rates per vehicle and per 100,000 miles.
Bridle also measures speeding, harsh braking and very harsh braking by unit. The worst offenders are offered counselling with regards to their driving style.
It’s no surprise that the number of speeding and harsh braking incidents has reduced by over 50% the past six to nine months.
“It’s a good news story for us,” says Bridle. “It’s a care and environmental issue – we take pride in the fleet. Drivers have to think about our customers’ perceptions” and our affect on the environment whilst they are out on the road.”
He believes the industry is moving towards developing more proactive driver risk management tools which will add value to Royal Mail’s products by providing its customer’s data in real time.
This includes electronic sign in to the vehicle and being able to identify speeding by road type. Additionally, engine management (CANbus) data will be used for more accurate measured readings, (rather than current GPS technology) especially where environmental, fuel and remote vehicle diagnostic’s performance data is concerned.
“In my view there is still an opportunity to improve performance in these identified areas by a further 15%,” says Bridle.
“For me it’s all about improving the driver’s attitude and behaviour – that’s where you will drive your further efficiencies, such as fuel saving, through a set of factual driver de-brief reports.
“We need to build a total picture of the driver, the vehicle and the journey for a live risk profile which will allow us to take appropriate action to improve performance.”
At least once a week, Bridle runs a Work Time Listen and Learn session with the worst performing units going through behaviour and defensive driving. The next stage is to measure the difference after the course.
“Any business that can accurately measure fuel, maintenance and accidents performance can compare and drive it down to reduce costs,” he adds. “That’s how you add value as a fleet manager.”
Road Safety - Royal Mail
- 24 February 2010
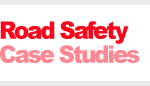
Brian johnson - 04/12/2014 09:12
How do i find and contact the person that does your job for the lincolnshire area